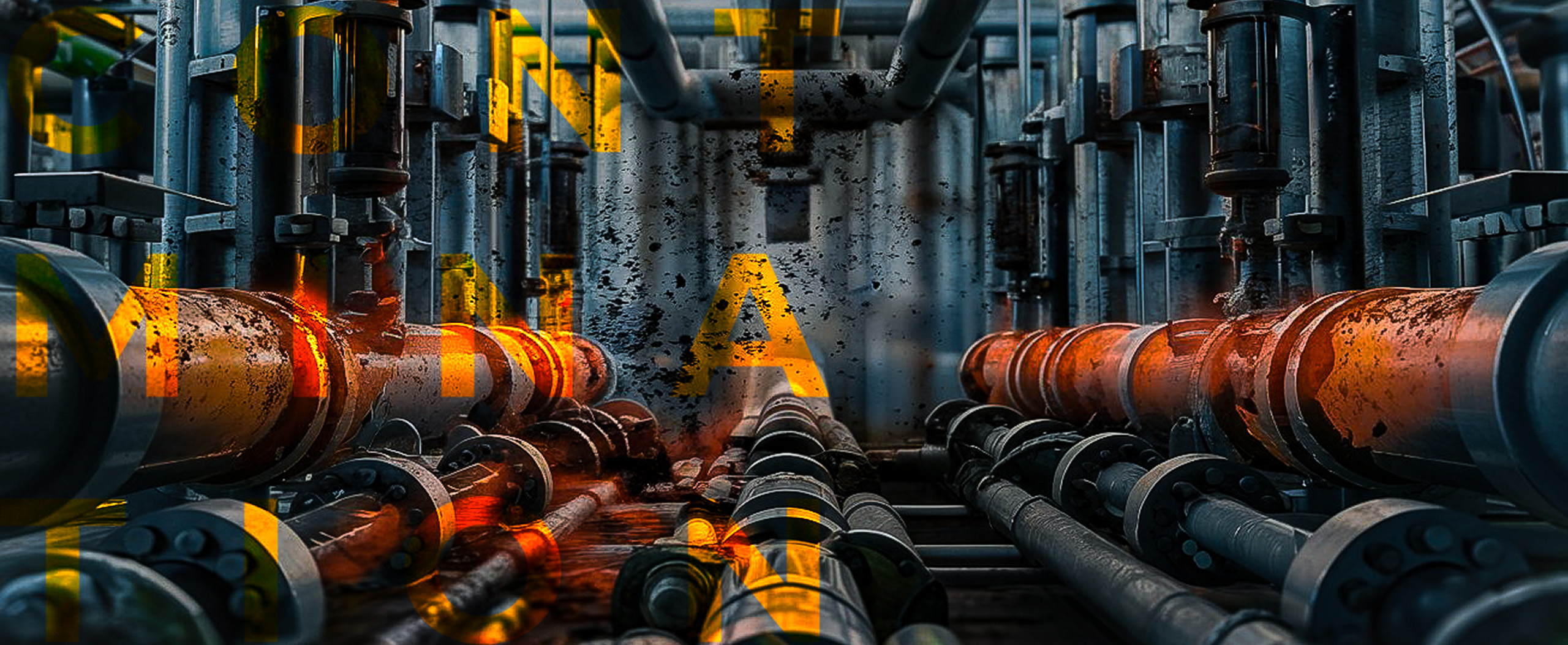
What is the correct contamination level for my hydraulic system?
This is a very frequent question for both planners and maintainers of hydraulic systems.
In the past, the choice of the required cleanliness level (RCL) was very often arbitrary, based on the experience of the designer or the recommendations of component suppliers, also based on experience.
The result was that the required level of contamination was often assessed subjectively and there could be significantly different assessments of the same system.
This generated uncertainty and confusion and often an incorrect RCL was chosen for the hydraulic system under consideration.
In an attempt to define an unambiguous method of assessing RCL, ISO Technical Committee TC131/SC6 developed a standard, ISO 12669, which allows RCL to be calculated for each hydraulic system.
The standard considers 6 different operating characteristics of a hydraulic system and for each of them provides guidance on their weight in the RCL calculation by means of special tables.
1 – Working pressure and work cycle
The maximum working pressure and the presence of cyclic pressure variations in the hydraulic circuit are rated on a scale of 1 to 8: the lowest rating is given to a system with low pressure and no pressure variations while the highest rating is given to a system working at high pressure and with considerable pressure variations in a short time.
2 – Sensitivity of different components to contamination by solid particles
On a scale of 1 to 8, the sensitivity to solid contamination of the various components in the circuit is assessed: for example, a gear pump is considered to be insensitive to contamination and gets a low rating, while a high-performance servo-valve is considered to be very sensitive and gets the highest rating. The rating of the system is equal to the highest rating obtained by the various components.
3 – Required service life
The required service life of a system is rated on a scale of 0 to 5; the lowest rating is for systems with a relatively short service life while the highest rating is for systems with a longer service life.
4 – Cost of any replacement of circuit components
On this scale, the cost of replacing a system component is rated from 1 to 4, both in terms of price and labour hours. Larger and/or particularly complex and expensive components usually have higher replacement costs and therefore receive a higher rating.
5 – Downtime cost
On this scale, from 1 to 4, the cost related to a possible system blockage is evaluated; for example, if production is not significantly affected by a system malfunction, the grade is 1, whereas if the malfunction generates a blockage of production with additional costs due to the presence of rejects, the grade will be 4.
6 – Human risks
The human risks related to a system malfunction are rated on a scale of 1 to 6. For example, in a passenger car, the risk to people related to a malfunction of the brake system is extremely high, resulting in significant damage, while a malfunction of the air conditioning system poses low risks.
Once the ratings for each of the above characteristics have been obtained, they are added together to obtain the RCL factor with which the RCL of the system can be calculated.
The standard provides a table correlating the RCL factor with the required contamination level (RCL) expressed as the ISO 4406 contamination code.
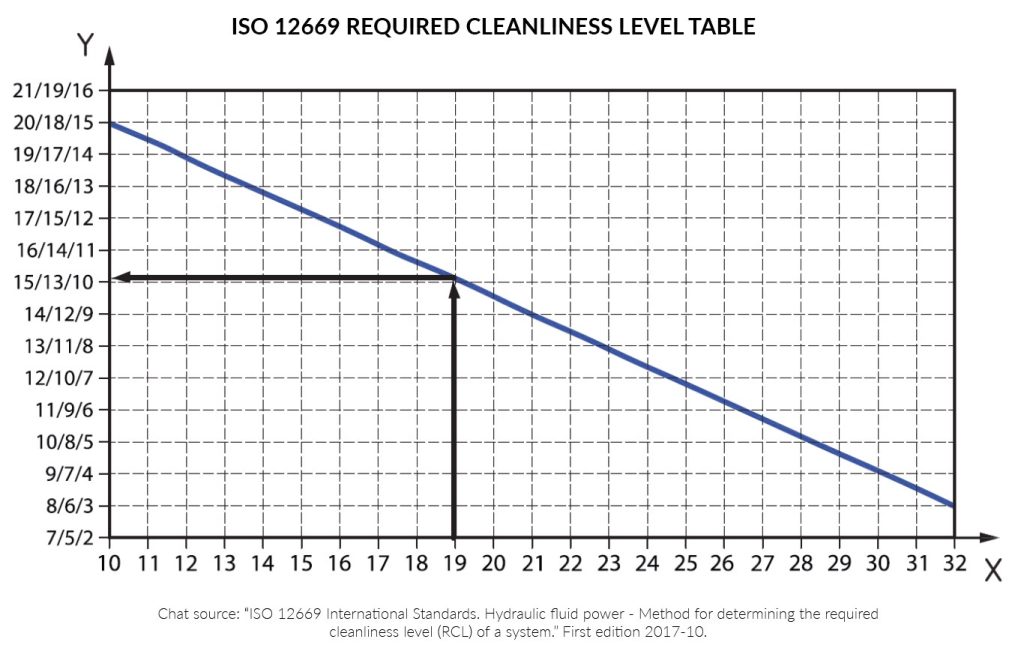
Thanks to this standard, all operators, from the designer to the maintainer, can unambiguously and objectively calculate what level of contamination is required by their hydraulic system and then take all the necessary actions to achieve and maintain it.
The Filtrec team of experts can help you determine the exact contamination level for your system and recommend the right products from our range to ensure optimal operation.
Contact us today to learn more about how ISO 12669 and Filtrec can help you achieve the ideal cleanliness level for your hydraulic system.